Manufacturing Success Stories
Lean Has Been No Shot in the Dark for Savage Arms Inc.
"It takes 213 quality controlled steps and the individual hands of 338 men and women to write the definition of accuracy." — Ronald Coburn, Chairman & CEO, Savage Arms Inc.
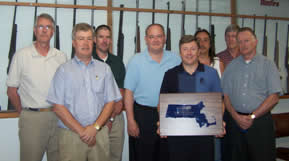 |
The Savage Arms Lean Team shown with an award
presented by the Mass MEP for successful
implementation of Lean methodology. |
Savage Arms is proud of their well-earned reputation for having the best out-of-the-box accuracy of any production rifle available at any price. After 113 years in business, the company manufactures in Canada and from their headquarters in Westfield, Massachusetts.
Meeting Increased Demand and Increasing Revenue by 78%
Savage Arms has been working on their Lean implementation with Mass MEP and its excellent team of resources for over 4 years. They have seen significant improvements in their overall operation and an increase in revenue dollars by 78%. Handling this kind of improvement, along with changes to nearly every part in their product line and the addition of over 150 new SKU’s this year alone, could have been unthinkable. By utilizing Lean tools, and continuing to change and improve, the dedicated workforce at Savage Arms has been able to meet growing demand and benefit from improvements like: increases in productivity, efficiency, profits, flexibility, speed, quality, on-time delivery, employee communications, and ownership.
Increasing Responsiveness, Operational Efficiency, and Process Improvement
In the spring of 2003, Savage Arms decided to develop a Lean Training and Implementation program as part of an ongoing effort to keep their competitive edge and grow successfully in the future. The company had already made significant gains on their overall performance by forming several continuous improvement teams which made a great foundation for their Lean Transformation. The focus was on increasing overall responsiveness, operational efficiency, and process improvement. Susan Janus, MassMEP Lead Project Manager was invited in to Savage Arms to conduct a Lean Assessment of their current processes. This allowed the Savage Arms leadership team and MassMEP to determine where their attention should be focused as they moved forward. MassMEP also assisted Savage Arms in successfully obtaining Workforce Training Grants to support the project.
Moving Toward an Ideal Future State
To get started, basic Lean Manufacturing Concepts (Time Wise LE101) were taught to the entire workforce at Westfield (approximately 360 people.) This training combines lecture and hands-on manufacturing simulation to illustrate the impacts of implementing Lean concepts on a simple manufacturing process. Next, Value Stream Mapping (VSM) was used to map out specific processes in the Receiver, Barrel, and Final Assembly Departments from beginning to end, and to identify areas of waste. Teams gathered current state data, including cycle times, changeover times, quality, equipment reliability, and travel distances to put together a picture (map) of their current state. Then, by looking at where the waste and other issues were occurring, they developed future state maps and corresponding implementation plans for improvement. Finally, the teams made presentations of their findings and strategies to senior management for their consideration and comments. The Value Stream Mapping workshops really got management and the workforce enthused. They were learning about internal customers and seeing how each job related to those before and after. It also made it easy for employees to share their ideas about how to improve their own processes.
Kaizen Events and other workshops were conducted over a four year period to address specific issues and non-value added activities. These events used a systemic approach (Plan, Do, Check, Act) to make the improvements and included: 5 S (Workplace Organization), Set-Up Reduction, TPM (Total Productive Maintenance), Cell Flow, Layout, and Pull Systems. Other specialized training workshops were conducted to help support the Lean Transformation process including: Problem Solving, Statistical Process Control, Internal Auditing, Inspector Metrology Training, and Performance Management / Employee Development.
Implementing the Changes – Seeing the Rewards
Using 2002 as a baseline the following impacts have been achieved:
- Productivity: Units produced increased 50% with same level of staffing and same facility
- Product Flexibility: 45% increase in number of SKU’s with a high level of new product introduced and processes developed
- Lot Size: Reduced by 50% +
- Production Lead Time: Reduced by 50%
A Lean culture has been created at Savage Arms with all employees participating in the events and implementing improvements. Operators are getting more involved by maintaining their own machinery to prevent breakdowns. Product is more efficiently moved through key process steps with a stronger tie to the "pull of the customer" – both internal and external. Visual pull systems trigger replenishment of vendor supplied parts and manufactured sub-assemblies, resulting in significant cost savings. Visual displays showing specific performance metrics (targets / actual) are posted. Lean concepts are utilized and their value recognized in Office Processes and in Savage Arms Supply Chain. Lean leaders help drive and sustain the change. Quarterly, Lean improvement teams present results to the senior management leadership team. Communication meetings are held with all employees on a regular basis. Savage Arms recognizes the value of ideas and suggestions from employees, customers, and other individuals and are known as the product innovator in their industry.
Significant Impacts and Sustained Improvements
Savage Arms attributes their success to their people. With strong leadership and commitment to their Lean Training and Implementation program, Savage Arms achieved significant impacts and has sustained the improvements made. Projects were done by teams made up of employees from a variety of departments who shared their skills, talents, and ideas, and then could take what they had learned back to their respective areas. These teams determined what needed to be done, took ownership of the changes, and drove the improvements. Savage Arms has succeeded because they started by making small gradual changes, putting the right teams together, working closely with their suppliers, communicating, and providing training for every employee. Over the last couple of years, they have reached beyond their own manufacturing facilities to extend the Lean initiative to their Supply Chain.
"The MEP has been a catalyst for the improvements that have taken place at Savage Arms. Two things I like about the MEP are that they are able to relate to all levels of the company from my level to the shop floor. I also like the way MEP works with our product and our people at our facility on site- within our world rather than sending people elsewhere and then having them try to come back and make it apply to their environment. It also took top level commitment from us (Savage Arms) to really get things going with the Lean Transformation." Al Kasper, President
The Best it Could Possibly Be
By the time Arthur Savage founded his namesake company, Savage Arms, in 1894, he had already enjoyed an intriguing life. This included developing a torpedo, being held captive by Aborigines in Australia, owning a cattle ranch, being a railroad superintendent, and, finally, inventing the first hammerless lever action rifle, the Model 99. This rifle included improvements that advanced technology, while at the same time, was affordable for the average person. The Model 99 was the first of many innovations that Savage Arms would provide to their customers throughout the years.
In 1919, Savage Arms was manufacturing high power rifles, 22’s, pistols, and ammunition. During the two World Wars, they produced and contributed millions of firearms including machine guns and heavy munitions. At that time, Savage Arms had become the largest firearms company in the free world. Even when production slowed, after WWII, they were able to shift some of their excess manufacturing capacity to building other products like the world’s first riding lawnmower. The next 20 years found the company bought and sold. After more than a century in business, Savage was losing money. When current Chairman and CEO Ronald Coburn arrived in 1988, there was much work to be done. He took the country’s largest manufacturer of rifles and shotguns and told them to forget about all the models they made – except one. Then he asked that they focus on manufacturing that one model the best it could possibly be done. Gradually they used this method to reintroduce each product back into the manufacturing process.
As the years have passed, new management has come to the company. Their contributions as well as the contributions of many talented team members and the incorporation of Lean Manufacturing concepts and continuous improvement into their processes have resulted in Savage Arms being recognized, once again, as the #1 long gun manufacturer in the country.
About the Mass MEP
MassMEP can assist your organization in a transformation from traditional to world-class manufacturer. Our experienced project managers will work with your team to identify conditions which may be impeding your ability to become more competitive and prosperous. We can assist in providing the resources to help you maximize your profit. In working side by side with your leadership, the MEP becomes a partner for success. Contact us at 508-831-7020.
|